Actuators are a vital component in a wide range of systems used in water, energy and other industries. But what exactly is an actuator? Newcomers to the topic are often content to think of this component as simply a switch, of sorts – the part of a valve-based system that brings the valve to an open or closed position. But the value of such parts increasingly goes beyond simple “open-close” functionality and into a realm where all kinds of sophisticated control becomes possible, as Envirotec discovered in conversation with AUMA Actuators UK, the UK arm of AUMA Group, which employs over 2,800 people in 30 locations wortldwide.
Valves have a vital role to play in systems where fluid (or gas) flow needs to be controlled. In applications where water flows through pipelines, for example, it might be necessary for the flow to be stopped, started, slowed, or for its direction to be changed. In some systems, valves will be called upon to regulate pressure in different places.
The water industry is a prime destination for these components, although they appear in a vast range of process technology and other systems, including power generation, whether it be from oil, gas, biomass, energy-from-waste, or nuclear. Actuators play a vital role in the control process.
Today’s electric actuators can be remotely controlled, and receive commands to open or close from industrial control systems like SCADA or DCS. Similarly, when the actuator has reached a particular stop or intermediate position, it will signal this status to the control system.
This kind of functionality is the baseline – and will suffice for many users – but much more sophisticated control is possible, and AUMA’s offering increasingly incorporates various kinds of ‘smart’ functionality. This is where an evolution of the technology around valves and actuators is most visible, suggests AUMA’s UK MD Paul Hopkins, who offered a sense of the possibilities coming into view with a subsystem that, he said, “is actually an exciting piece of engineering”.
What does it do?
AUMA’s electric actuators feature a combination of an electric motor and gearbox, specially developed for valve automation. Actuators provide the torque needed to operate the moving parts of the valve, whether it be gate, butterfly, globe or any other type of valve. As AUMA’s website states, the firm’s actuators address the entire range of possibilities, from a 2-inch ball valve to diverter dampers many metres high (see “Valves: the basics”, at the end of the article, for more on valves).
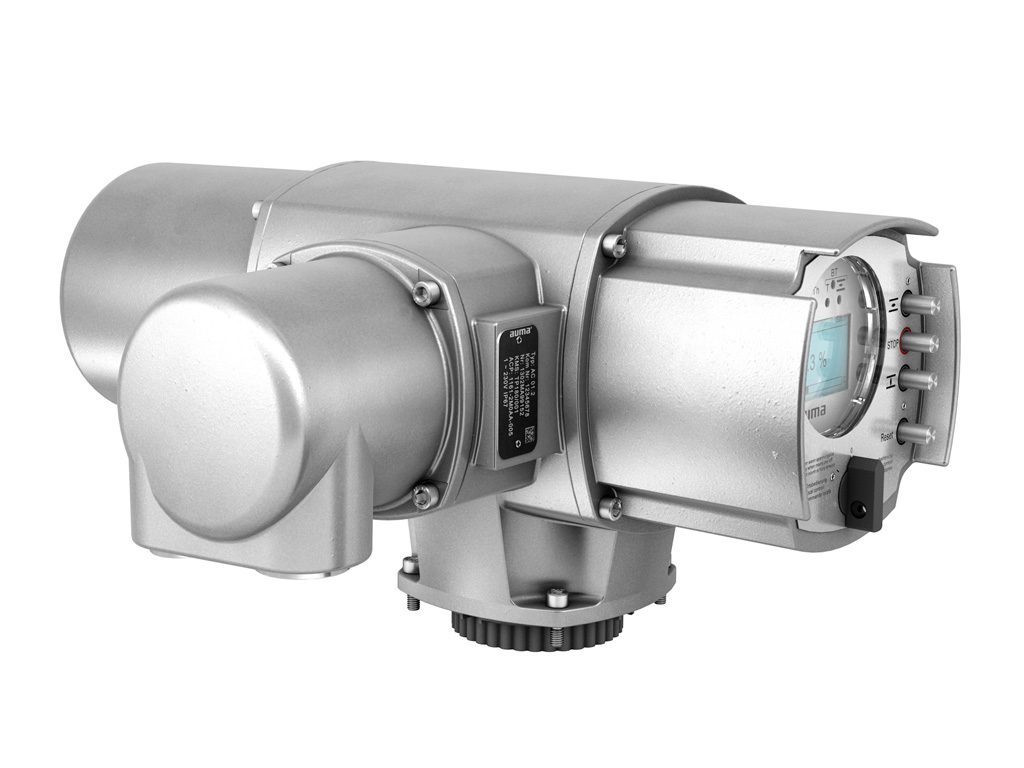
The torque is transmitted from the actuator to the valve stem or shaft via a standardised mechanical interface. So the type of valve determines the choice of actuator, with actuators available as “part-turn” or “multi-turn” devices.
The part-turn actuators only require a small amount of rotational movement (less than 90 degrees) to open or close the valve, and tend to be used for valves operating in a quick on/off fashion. The multi-turn actuators apply multiple rotations to the valve stem to fully open or close the valve, and are used where the valve positioning needs to be precisely controlled, as with gate, globe or rising stem valves.
Sometimes it’s important to carefully control the torque applied when opening or closing a valve, to avoid damaging the valve or the process it’s controlling, explained Hopkins. Actuators also provide the interface between the valve and control systems (and intelligence embedded within the wider system), and this aspect is becoming increasingly important with trends such as IIoT and Industry 4.0.
AUMA provides the baseline level of control functionality in its AM range of actuator controls, and these parts are said to be the perfect choice where you simply want to be able to report the actuator’s end position and fault signals (which are also visibly displayed by lights on the unit). Additional control functions are possible with the firm’s AC range of controls, said to be a suitable choice where you need data logging, or self-adapting control functions, or where the valve-actuator is integrated within a system equipped for things like asset management and remote maintenance. The part incorporates microprocessor control, providing much more comprehensive functionality says Hopkins, as well as the option of connecting it to process automation via Fieldbus (parallel interface is also available, as with the AM controls).
The AC unit also provides functions such as torque bypass, to un-seat valves that are tightly seated, and functions to help with avoiding water hammer in pipelines. Hopkins situates parts like these within the Industry 4.0 paradigm, and the three layers of the control system: the sensors (“to tell you what’s going on”), the process controller (“to tell the system what it should be doing”) and the physical layer or output devices. Actuators fit into this last level of the system.
Various diagnostic functions are provided by the AC, including a time-stamped event report, and logging of torque characteristics, as well as the number of starts and motor running times. Continuous monitoring of temperature and vibration is a feature that can help end users to keep their plants running reliably, suggests Hopkins, offering a fit with modern water industry aspirations for “no outages” and so on.
Tackling water hammer
Much discussed in the water industry at present is the subject of leakage, and more than 1 trillion litres of potable water was lost via leaky pipes in England and Wales in 2021/22, as a recent AUMA video explains. The same presentation explains how variable speed actuators can be programmed to help calm the water network, avoiding the damage caused to pipes by sudden transient surges. This “water hammer” effect arises when valves close suddenly or at high speed, producing a high-pressure wave that propagates through the network, putting stress on valves, seals and mechanical components, while also sometimes damaging pipework.
One solution is to vary the speed at which these valves open or close, in an intelligent way, taking into account the overall effect on pressure-change dynamics throughout the network. AUMA’s variable speed actuators can be programmed, and the valve travel (in both opening and closing directions) can be divided into ten di erent sections, with it being possible to specify different speeds for each.
This kind of solution can be used within a water network equipped for monitoring, analysing and acting upon pressure transients, reducing the likelihood of asset damage.
Putting parts together
In the real world, valve-actuator systems seem to fall across a spectrum of sophistication and complexity, and AUMA product range is built using a modular design philosophy, which is usefully geared towards addressing the unique requirements of specific users.
On one level, says the firm, the modular product design supports things like easy retrofit and repair, and systems can be easily upgraded from AM to AC controls, for example (and backward compatibility is preserved too). The approach also makes it easier to provide the optimal combinations of components within the actuator (such as gearboxes and linkages), tailored to the situation, and the best ways of coupling them. Possibilities include closer
coupling of valve and actuator (rather than only using universal joints), and having parts like the gearbox and motor separately located from the controls – for example, at height, or down a pit, or even underwater. One example of where this came in handy was with an underwater hydro turbine control application at the Sauerbrunn hydropower plant near Graz, Austria, in Autumn 2022, resulting in a solution that provided better control and feedback at a much lower cost.
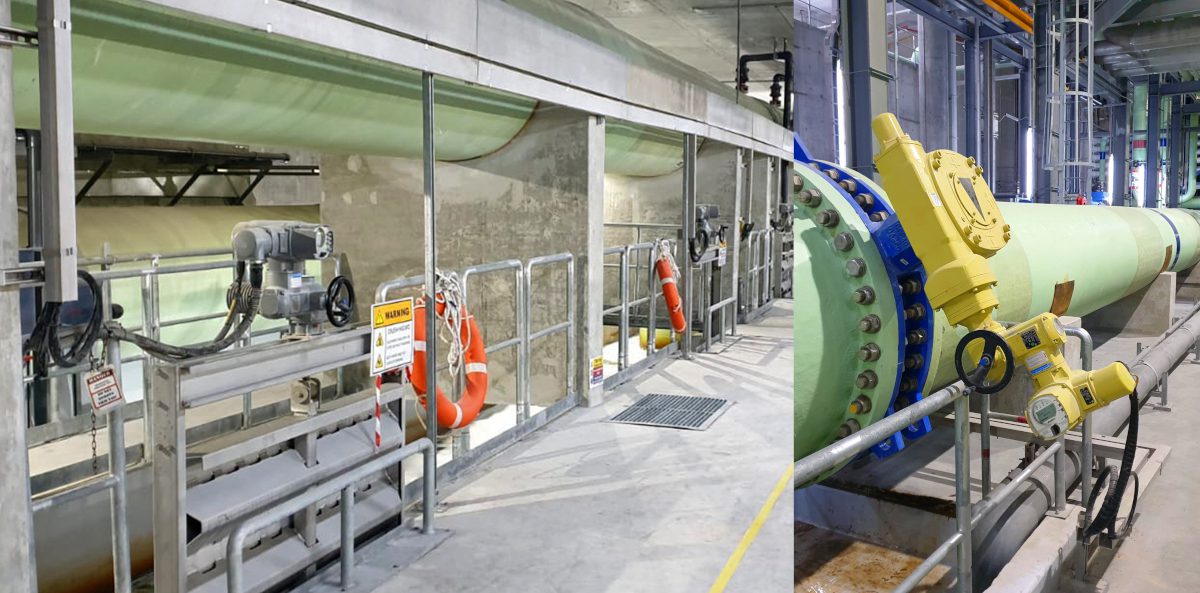
The system required an actuator able to operate continuously underwater, to provide accurate positioning of the turbine, to optimally control the water supply it received. The only option previously had been a hydraulic actuator, but AUMA was able to suggest an electric actuator suited to underwater use (the AUMA SARV-UW), in combination with actuator controls mounted above the shaft and separately from the actuator (and above water).
Different environments
A modular solution can select from parts specified to cope with particular environments. While broadly similar technologies are used across sectors like oil and gas, EfW, and nuclear power – in terms of the valves and actuators used with boilers, for example – some sectors present specific demands. Oil, natural gas or EfW plants will require parts to be explosion-proof, for example (AM and AC products are available in this form).
Certification is of the utmost importance in the nuclear sector, said Hopkins, and parts are distinguished by things like the level of certification, the sourcing of materials, and the machinery or housing used with the product.
AUMA has an interest in both the emerging field of small modular reactors (SMRs) and also larger projects such as Hinkley Point C. Corrosion protection is important in sectors like water, where equipment might need to sit outside, in the presence of saline, coastal air. AUMA has developed its own solution here, which is supplied as standard, for example, on its PROFOX actuators, used recently in conjunction with butterfly valves at Penybont Water Treatment Works on the midWales coast. The corrosion protection meets the highest C5-M/ C5-I requirements of EN ISO 12944-6.
Easing the load
The modular design philosophy seems to be a key underpinning numerous things that can make life easier for the end user. For example, in situations where it makes much more sense to take a mostly prefabricated solution to a site, rather than assembling it all in situ. Doing o site work also helps keep things safe, says Hopkins, so electrical work can be carried out separately, and at a different time, from the rest of an installation, for example.
A lot of flexibility is available to spot opportunities to improve or upgrade an end-user’s equipment, he suggests. One of the biggest points of failure in the water industry, in his own analysis, arises from the shaft in a penstock valve not being properly greased.
He said AUMA’s engineers focused on this spot with one water utility customer, providing an autogreaser that not only greases the bearings but also feeds into the drive base and greases the shaft. A change like this, says Hopkins, “is simple, but potentially saves hundreds of thousands of pounds on the penstock” and greatly decreases the number of times it will have to be serviced.
This kind of “consultative sell” appears key to the way the company works, and it relies on engineering expertise. Parent company – AUMA – has been developing and building electric actuators and valve gearboxes for 60 years. The large network of offices around the world means engineers in the UK can draw on the expertise of others, who may have experience of solving a particular type of problem.
The last few years have also seen a great deal of turmoil with materials, production and supply chain issues, says Hopkins, and navigating this territory has been helped by AUMA’s being “very vertically integrated”, with sites like the Clevedon o ice of AUMA Actuators Limited doing its own machining, assembly, test and repair.
The parts themselves are manufactured in Germany, with factories operating in a “kanban” system, pulling demand through rather than holding stock. As far as capacity goes, Hopkins says the firm builds more than 500 electrical actuators to order every day.
[ SIDE PANEL ]
Valves – the basics
Valves come in all shapes and sizes, with different approaches available to suit specific needs, in terms of things like cost, speed, reliability and so on. Some applications require the valve to be simply opened or closed, while in others you might wish to hold it in various intermediate positions, to regulate the fluid flow.
One common practice is to divide the world of control valves into parts based on linear motion (gate, globe, and diaphragm valves), vs those based on rotary motion (ball, plug and butterfly valves, for example). Gate valves are the most common in use today, given their relative simplicity and low cost. These can be used to start and stop fluid flow, but not to throttle it. Gate valves aren’t suitable to throttling flow, and can be subject to vibration when left in a partially-open position. They are also more likely to su er seat and disc wear, and leaking, compared to globe valves, for example.
[ END OF SIDE PANEL ]
