Peter Smith, Sludge Treatment expert at waste management company CSG, lifts the lid on the new sonar technology the company is using to accurately calculate how much sludge or silt is present in a body of water before removal.
Lagoons, oxidation ditches and settlement ponds are established methods of clarifying waste waters from a variety of industries. Gravity settlement is nature’s way of water clarification, but nothing is perfect.
The settled solids do not just disappear but merely accumulate on the bottom of the lagoon. The problem with this is the settled solids are in a layer and can be spread over the entire area of the lagoon – and this makes monitoring of the silt accumulation extremely difficult.
As sludge accumulates the capacity, and therefore the residence time, within the lagoon is reduced, which can result in failures of the discharge consent.
To avoid this, the lagoon owner needs to know how much silt there is and the rate at which it is increasing. If they know this, dredging operations can be carried out before the situation becomes critical.
This is where the CSG Sonar Service is invaluable. Originally developed to monitor silt build up in crude oil storage tanks, we have now adapted the technology so it can be used on any body of water.
Weighing just 25kg and easily deployed by a two-man sonar team, the Sonar Catamaran maps the surface of the layer of the silt in any lagoon. It is battery powered with two small turbines and is operated remotely from shore.
We can use this mapping technology to allow more accurate estimates of the quantities of material that would be produced by dredging. The disposal can be the costliest part of the project – often running into tens or even hundreds of thousands of pounds – and it is critical that the client has a good understanding of these costs before entering into a contract.
Without sonar technology, judging the depth of the sludge is a fairly primitive and inaccurate exercise, often involving a long dipstick.
A sonar survey can be carried out before and after a dredging project, so the results are clearly visible to the client.
Some clients choose to monitor the silt build up with a regular survey on an annual basis. Most surveys can be done within the day but, obviously, the larger the lagoon the longer it takes.
In simple terms, a sonar survey on a large lagoon will show the depth of clean water above the sludge and this data is used to produce the 2D image of the silt surface.
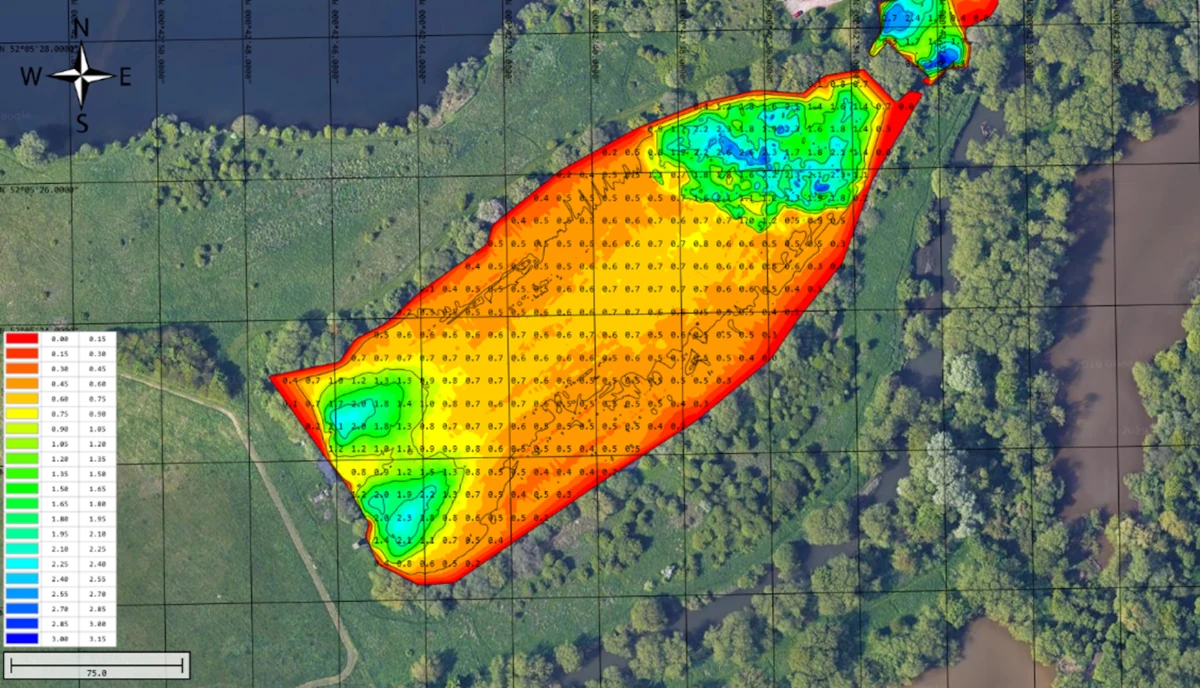
For example, the maximum depth of the lagoon might be three metres, but in most areas the water might only be 0.7 metres deep. The problem is clearly demonstrated in the mapping image and in this case dredging work would be urgently required.
Once the volume of silt to be removed is known, the whole project is estimated and dredging can begin.
Using a remote-control amphibious dredger, the silt is pumped to shore where it is dewatered and turned to a solid cake for removal from site. The remote-control dredger dramatically increases safety by eliminating humans on the water – and reduces costs for the customer as it removes the need for a two-man rescue team to follow the dredger.
And by using the sonar device beforehand, we already have a very good idea of where the largest build-ups are, improving efficiency.
Several methods are used to dewater the sludge and the site circumstances usually dictate the most efficient method. Unlike other suppliers, we use geo bags, centrifuges or screw press to reduce the water content of the silt to a point where the solids can be transported in bulk tippers.
Geo bags are large, permeable fabric containers filled with silt and water. They are used to reduce the water content of silt by allowing water to drain out through the fabric while retaining the solid particles inside. They prevent erosion and minimise contamination – but they can take up considerable space.
Centrifuges reduce the water content of silt by rapidly spinning the mixture in a cylindrical drum, utilising centrifugal force to separate solids from liquids. As the drum rotates, denser silt particles move outward, while water is forced inward and drained away. This process effectively dewaters silt, producing a drier, more manageable material.
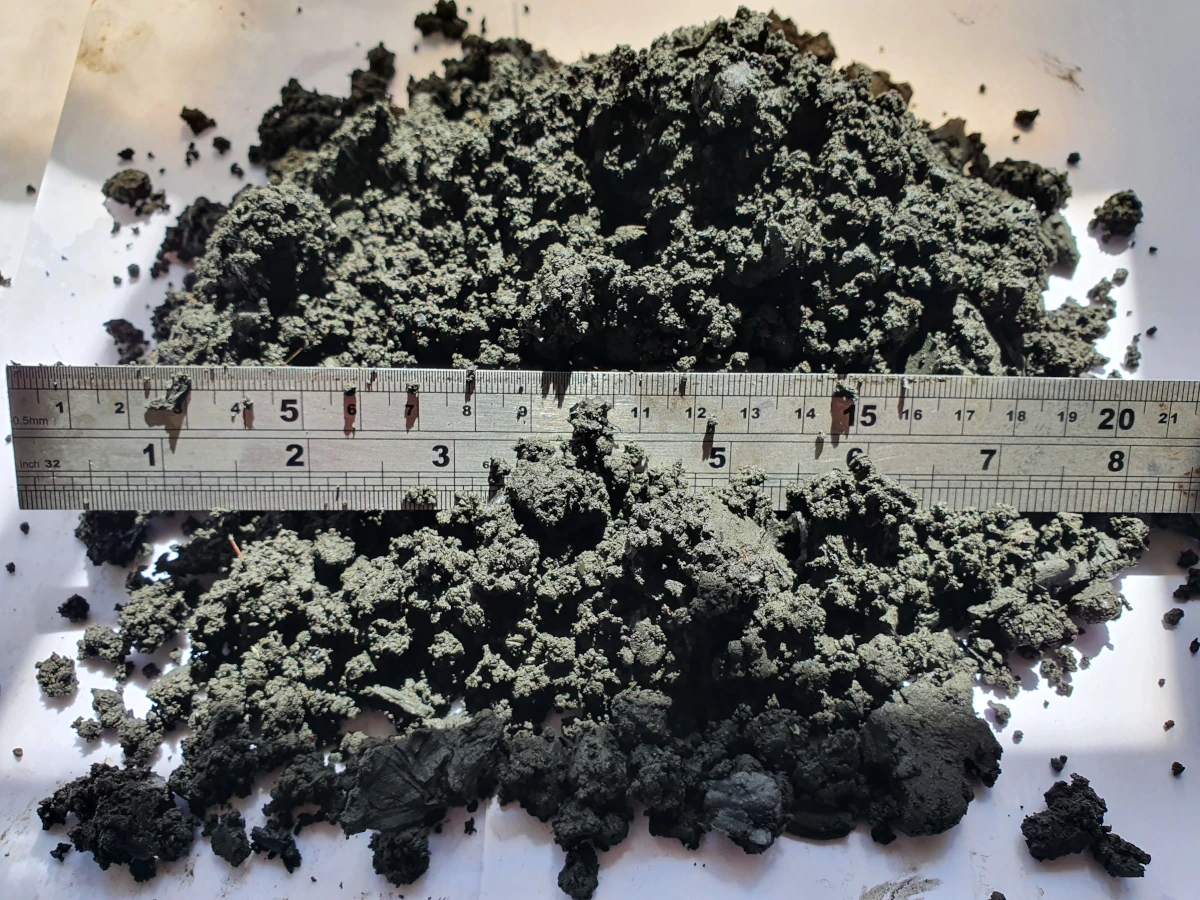
Screw presses reduce the water content of silt by using a rotating screw mechanism within a cylindrical screen. As silt is fed into the press, the screw advances it along the screen, compressing the material and forcing water out through the screen’s perforations.
We believe the use of sonar technology could transform the way in which sludge build-up in settlement ponds and lagoons is monitored and maintained. We also see uses in boating ponds, backwash ponds and ponds for final polishing. In fact, we recently worked on a boating pond which was almost half silt!
Don’t ignore sludge or silt – speak to the experts.
